6.成形加工
分野別ページ|建築・土木
6. 成形加工
アルミニウム材料には純アルミニウム,Al-Cu系,Al-Mn系,Al-Si系,Al-Mg系,Al-Mg-Si系,Al-Zn-Mg系などの各種合金があり,各合金系でおおむね表3に示す特性がある。
アルミニウム材料はその合金の種類により,機械的性質,加工性,および耐食性がいちじるしく異なり,アルミニウム材料採用に当たっては,十分その特性を理解して選択する必要がある。
アルミニウム材料の選択は,つぎの各項目について行う。
・機械的性質……引張強さ,耐力,硬さ,伸び率
・加工性…………曲げ性,プレス性,溶接性,ろう接性,切削性などの要求項目
・表面処理性……塗装,化成処理,陽極酸化処理(アルマイト),光輝処理性,メッキ性などの要求,仕上げに対する検討
・耐食性…………使用環境に適した耐食性
・その他…………耐熱性など
・価格
アルミニウム材料の成形性はきわめて良好であり,せん断,曲げ,プレス,絞り,ロールフォーミングなど多くの成形加工法が適用される。
アルミニウム材料はその合金の種類,質別により加工性が異なり,一般的に建材用としては非熱処理合金の純アルミニウム(1100,1050),Al-Mn 系合金(3003,3005等),Al-Mg系合金(5052,5005等)の耐食性,加工性の良好な材料が使用されている。主にアルミニウム建材に使われる加工は以下の通りである。
1. せん断加工
せん断加工は材料にせん断荷重を加えて分離する加工法であり,切断,打抜き 穴あけ,切込みなどに分類される。
せん断には金切り鋏,押切り,切断機やプレス,丸鋸,ジグソーなどを用いるが,作業量,寸法,形状によって適切な工具,機械類を選択する。
手切り
金切り鋏は通常1mm以下の薄板切断に使用する。鋏は常に板の面に垂直に保ち,歪みを生じないように注意する必要がある。切欠き状に切るときは,交点を越えて切り込まないこと。できれば交点に2mm程度の小穴をあけておくと交点からの割り込みがなく,仕上がりがよい。曲線に切るときは,えぐり鋏を使用する。
電動鋏切り
最近電動工具が開発され,刃先に往復運動を与えて切断する方式が採用されている。この方式に2種あって,シングルカット方式即ち手持ち金切り鋏を単に動力掛けとしたものと,ダブルカット方式即ち切り落とし部分が一定の幅のスクラップになるものがある。ただし,これらも万能ではなく,形板の形に直角方向の切断,立ち上がり部分の角の切断には金切り鋏などの手動切断を併用する場合が多い。
せん断切り
せん断機にはギロチンせん断機,両切せん断機,丸切せん断機,自動せん断機などがある。ギロチンせん断機は直線切断に用いられ手動式,足踏式,電動式があり,刃に沿って押板のついたものを用い正確な寸法の切断ができる。しかし,同一材料でもクリアランスや拘束条件により,切口面形状が変化する。一般的にはクリアランスは板厚の5~10%が適当である。
両切せん断機は一定巾の板を多数切断するのに適している。
丸切せん断機および自動せん断機は,曲線状に板を切断するのに用いられる。
鋸切断
鋸には丸鋸,帯鋸,弓鋸の3種類がある。鋸の目にわずかな傾斜と前すくい角をもつ,鋸の刃巾の切代があるので,それを見越した寸法取りをしなければならない。一般的にアルミニウムの切断には目づまりを防ぎ,切れ味を良くするため,刃先角は逃げ角を大きくし比較的粗く付けたものが良いとされているが,薄板の切断には不向きである。潤滑油は一般機械切削と同様に,切削油および粘度の低い鉱物油が適当である。
打抜き
打抜きによって所望の製品を得る加工法である。ダイスとポンチのすき間は,薄板もしくは精度を要する場合は,板厚の2~4%が適当である。最大すき間は0.5mm程度とする。ポンチとダイスの芯は正確に保持する。芯に狂いがあると製品の精度を悪くし,“かじり”を生じて型を破損したりする。
穴あけ
穴あけは,打抜きとは反対で製品に所要の穴をあける加工法でパンチ加工とドリルによる錐もみがある。穴あけ作業は穴の寸法,形状,材料の板厚,穴あけの目的によって使用工具が異なる。接合を目的とした穴あけの場合には形状・寸法・穴ピッチの精度および穴抜きの“かえり”に注意する。
【パンチ抜き】
穴の位置はあらかじめポンチで目打ちあるいはガイドを設け,正確な位置に穴あけをする。普通,一個ずつあけ,穴の間隔が一定であるときは数個のパンチを一型でつくり穴あけをする。パンチとダイの間隔は板厚の5%以下にする。
【錐もみ】
ハンドドリルと機械ドリルによる場合とがある。穴の径が板厚より小さいときはハンドドリルによる。機械ドリルには胸当てドリルと電気ドリルがある。錐もみの際,薄板ではドリルの押しつけによる板の変形がおきやすく,穴がきれいにあかない場合があるので,その際は平らな台木をおいて,その上から作業をするとよい。また,錐が貫通した瞬間,ドリルチャックがアルミニウム材に当たって傷をつけることがあるが,これを防止するために根元にゴム座をはめておく工夫も必要である。潤滑油を使用する場合は,切削油または鉱物油を用いるのがよい。
表8 せん断機と切断可能な板のサイズとの関係
| | |
(mm) | (mm)
| |
|
| |
| | |
| | |
| | |
| |
表9 鋸の目数と送りおよび削り速度
| 目/10cm | (cm/min) | (cm/min) |
4 ~8 | 軟質:40~60 硬質:10~40 | 1,400~3,800 | |
板厚2mm以下:43 4mm以上:28 4mm以上:16~20 | 5~10 | 約2,400 1,200~1,700 約 780 | |
20~40 | 約40回/min |
表10 クリアランスの実用値(数値は板厚×%)
|
|
|
|
| | | |
| | | |
2. 曲げ加工
板の曲げ加工は,折台,拍子木,影タガネ,刀刃などを用いて,叩いて曲げる手加工とベンダー,フォーミングロール,あるいは3本ロールなどを用いる機械加工とがある。
機械加工では,一般にベンダーが多用されている。ベンダーには多種の曲げ型が用意され,V曲げ,U曲げ,端曲げ,波曲げなどほとんどの折曲げ加工が可能である。
近時はNC制御によるベンダーが一般的となり,寸法精度の向上,安定化および省力化と作業効率もよい。
曲げ加工に際して,材料が曲げ型にあたる板面をマスキングフィルムなどで保護すると,当たり傷,すり傷が防止されると同時に施工取付け時のハンドリング時に発生する傷防止にも有用である。
アルミニウム板の曲げ性での圧延方向による差異は,他の金属にくらべ少ない。
アルミニウム板の90度曲げの最小曲げ半径の値を表13に示す。
表11 錐もみの刃先角とねじれ角
| | |
| | |
| | |
表12 曲げ加工機械の種類と特長
| |
| 2.厚板加工に利用される |
| |
| 2.大量生産向き 3.長尺物の曲げに適す |
表13 アルミニウム材料の冷間90度曲げ加工の最小曲げ半径
材 質 | 各板厚に対する曲げ半径 (t:板厚) | |||||
0.4mm | 0.8mm | 1.6mm | 3.2mm | 4.8mm | 6.4mm | |
1100-O,5005-O 3003-O | 0 | 0 | 0 | 0 | 0.5t | 1t |
1100-H12,5005-H12 1100-H14,5052-O 3003-H12,6061-O | 0 | 0 | 0 | 0.5~1t | 1t | 1~1.5t |
3003-H14,5052-H32 5005-H32 | 0 | 0 | 1t | 0.5~1.5t | 1~1.5t | 1~1.5t |
1100-H16,5052-H34 5005-H34,7075-O | 0 | 0~1t | 0~1.5t | 1~2t | 1.5~2t | 1.5~2.5t |
3003-H16,6061-T4 5005-H16 | 0~0.5t | 0~1t | 1~1.5t | 1.5t | 2.5t | 3t |
1100-H18,6061-T6 5052-H36 | 1t | 1t | 1.5t | 2.5t | 3t | 3.5t |
3003-H18,5052-H38 5005-H38 | 1t | 1.5t | 2~2.5t | 2.5~3t | – | – |
【スプリングバック】
スプリングバックは,曲げ加工品の精度を考えるときもっとも重要な問題である。金属材料には,曲げ加工で材料に力を加えて変形させたあと,力を除くと材料の弾性力のため,形状がもとにもどろうとする性質がある。これをスプリングバックという。
このスプリングバック量はアルミニウム材料の種類と質別により異なり,板厚が薄く,耐力が高い程大きい。従って同材質ならば質別はH1nの方がH2nより大きい。成形条件としては曲げ半径,曲げ角度が大きく,ダイス肩幅がせまいほどスプリングバックは大きくなる。加工機械と金型も影響する。対策としては,実験または実作業でその量をあらかじめとらえておいて,その分量だけ余計に曲がるオーバーベンドをすれば問題ないが,実際にはこのスプリングバックの量が一定にならないでばらつきが生じる。このばらつきには,材料板厚,機械的性質などの変動が影響する。
これらのばらつきを一定にすることは難しいので,加工方法,作業方法で手加減して解決している。アルミニウム板材料では同一製造ロット内でのこれらのばらつきは非常に小さい。
厳しい精度を要求される場合,素材の面で材料内の応力分布の均一化をはかる目的で板材の引張矯正を行うことも効果的である。
図2に代表的なアルミニウム板の90度曲げでのスプリングバック例を示す。
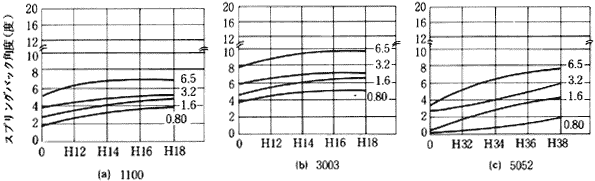
図2 アルミニウム板の90度曲げにおける曲げ半径とスプリングバック角度
(板厚1mm,図中の数字は曲げ半径)
3. ロールフォーミング
ロールで成形する方法はいろいろあるが,長いアルミニウムの帯板を上下一対に組合せ直列に配置された何組かの成形ロールの間に通して,ロールの回転により帯板を送り出しながら各々のロールで少しづつ所望の形状に曲げ加工を行って目的の断面形状に成形する加工方法をロールフォーミング(Roll Forming)という。
短い曲げ製品はベンダーで加工できるが,長尺ものはこの加工法に限られる。ロールによる連続加工方式で非常に生産性に優れ経済的であり,多量生産に向いている。
アルミニウム材料は鋼板やその他の材料に比べ変形抵抗が低いから,一般には鋼板の加工に使用されているロールフォーミング設備や成形技術をそのまま適用でき,しかも鋼材よりも高速加工が可能である。25~30m/minの速度が一般的である。その中で気を付けなければならないことの一つは成形機の成形ロールの表面はできる限り滑らかに研磨することが重要である。又そのロール表面に硬質クロームメッキ処理を行うことによって製品への加工中に発生する傷を防止し,製品寸法精度,品質の確保とロールメンテナンスの省力化がはかれる。
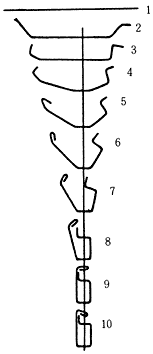
図3
ロール設計上の問題点として,アルミニウム板が通過中,板のせん断や破断しがちな鋭い端や角をさけ,製品のひずみ,割れをさけるため,各ロールスタンド間で過度の加工をしないで,平均して徐々に曲げ成形をするよう,ロール形状とロール段数を決定する。一般にアルミニウム材料では,一段のロール通過での曲げ角度は22度以下に設定する。成形過程断面図を図3と図4に示す。
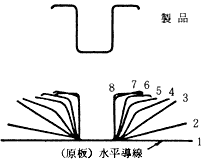
図4
4. プレス成形(絞り加工)
絞り加工とは,上型(ポンチ)と下型(ダイス)を用い所要形状に絞り成形する加工法である。プレス成形の基本構成を図5に示す。プレス成形における成形区分は図6に示すように,深絞り,張出し,伸びフランジ,曲げの4種の基本成形に分類される。絞り加工には一般的用途として1000番台の純アルミニウムがもっとも多く使用されているが,建材用には5052合金や3005合金も使用されている。
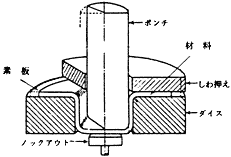
図5 プレス型の基本構成
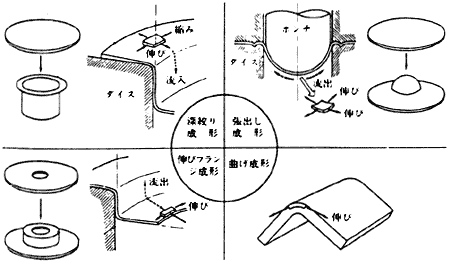
図6 プレス成形の基本的な分類
5. エンボス加工
エンボス加工は凹凸模様のあるロールを使用して,連続的にロールの模様を板に転写する加工である。このエンボス加工には両面エンボス品と片面エンボス品とがある。用途として足場板や,サイディングに多く使用されている。